PRODUCTS switch button
DLC coated carbide cutter for non-ferrous materials

The AE-TS-N and AE-TL-N carbide cutters with DLC coating are extremely effective for non-ferrous materials such as aluminum alloys that require weld resistance and high lubricity with DLC-SUPER HARD coating. With excellent cutting sharpness, these cutters are capable of eliminating burrs for an excellent surface finish. This range of cutters is available in straight, sharp edge and radius types to accommodate a wide range of possibilities from part processing to aerospace applications. Also, day. 1 mm to 2.5 mm has been added to Line for straight type and sharp edge type to support precision machining of small diameter sizes.
High performance type DLC coated carbide cutters (AE-VTS-N) for non-ferrous materials is also available.
Learn more

Characteristics

1 DLC-SUPER HARD Coating
2 Tip edge geometry stiff and sharp
3 New flute shape allows excellent chip evacuation

4 Center cutting edge specification allows plunge milling
• Wide core design with high rigidity to prevent chattering
• With sharp edge: for milling straight edges without burr
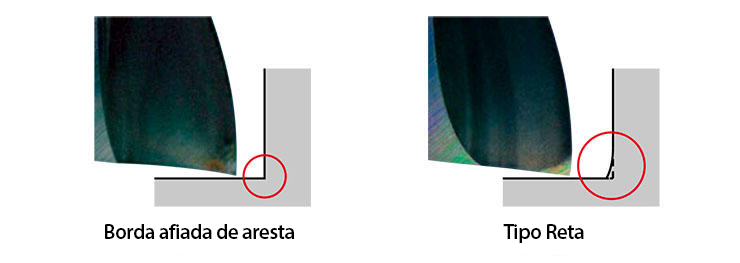
Aplicações
Copper alloy・Aluminum alloy・Plastic
Produtos
Short Type (AE-TS-N) 1.5 x D Channel Length (Neck Length 3 x D)
- Straight type φ1×3~φ25×75
- With radius φ3×9×R0.2~φ12×36×R3
- With sharp edge φ1×3~φ12×36
Long type (AE-TL-N)
- Straight type 3×D channel length φ3×9~φ25×75
- Straight type 5×D channel length φ3×9~φ25×125
- With sharp edge 3×D channel length φ3×9~φ12×36
- With sharp edge 5×D flute length φ3×9~φ12×60
Others
- Also available: high performance cutter (AE-VTS-N), for deep tangential milling (AE-VTFE-N) and carbide cutter with DLC coating for non-ferrous materials.
- Details on high performance cutter(AE-VTS-N)< /li>
- Details on high performance cutter for deep tangential milling(AE-VTFE-N)
Dados
Results of combining DLC coating and unique cutting edge geometry for machining non-ferrous metals
Considerações Ambientais
Long tool life with DLC coating
Extending tool life leads to reduced waste, which helps conserve resources. Furthermore, a recycling-oriented manufacturing system is possible through re-sharpening tools, re-coating tools and recycling materials.